
SIMATIC STEP 7 PLC SIMULATOR FOR WINDOWS 10 KEYGEN

Repetition of length of protocol data unit, (Hamming distance = 4)įrame Checking Sequence, calculated by simply adding up the bytes within the specified length.

They can be differentiated by their start delimiter (SD): The master signals the start of a new telegram with a SYN pause of at least 33 bits (logical "1" = bus idle). There may not be a pause between a stop bit and the following start bit when the bytes of a telegram are transmitted. In a PROFIBUS DP network, the controllers or process control systems are the masters and the sensors and actuators are the slaves.Įach byte has even parity and is transferred asynchronously with a start and stop bit. The data link layer FDL (Field bus Data Link) works with a hybrid access method that combines token passing with a master-slave method. DP-V2 for isochronous mode and data exchange broadcast ( slave-to-slave communication).DP-V1 for acyclic data exchange and alarm handling.DP-V0 for cyclic exchange of data and diagnosis.To use these functions, various service levels of the DP protocol were defined: PROFIBUS Protocol ( OSI reference model) OSI-Layer 5 million of these are in the process industries. In excess of 30 million PROFIBUS nodes were installed by the end of 2009. This means that DP and PA can work tightly together, especially in hybrid applications where process and factory automation networks operate side by side. The much faster DP acts as a backbone network for transmitting process signals to the controller. However, PA uses the same protocol as DP, and can be linked to a DP network using a coupler device. PA has a data transmission rate of 31.25 kbit/s. The number of devices attached to a PA segment is limited by this feature. the cable) conforms to IEC 61158-2, which allows power to be delivered over the bus to field instruments, while limiting current flows so that explosive conditions are not created, even if a malfunction occurs. This variant is designed for use in explosion/hazardous areas ( Ex-zone 0 and 1). PROFIBUS PA (Process Automation) is used to monitor measuring equipment via a process control system in process automation applications.The many standard diagnostic options, in particular, are focused on here.
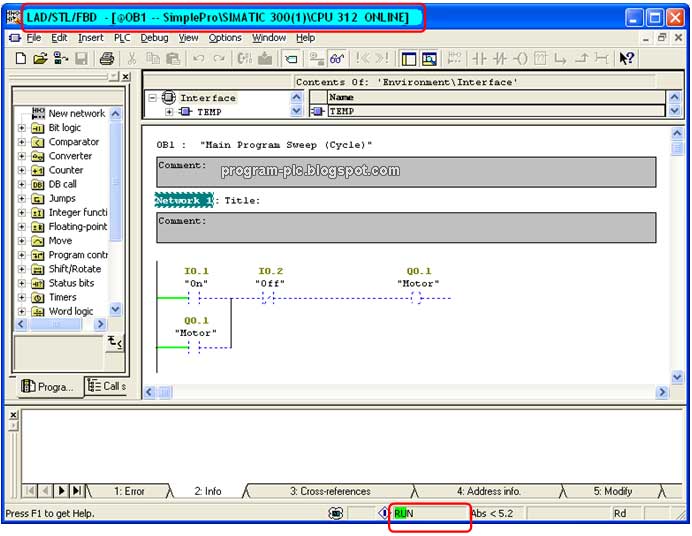
PROFIBUS DP (Decentralised Peripherals) is used to operate sensors and actuators via a centralised controller in production (factory) automation applications.There are two variations of PROFIBUS in use today the most commonly used PROFIBUS DP, and the lesser used, application specific, PROFIBUS PA: Profibus DP is a protocol made for (deterministic) communication between Profibus masters and their remote I/O slaves. Profibus FMS is used for (non-deterministic) communication of data between Profibus Masters. Subsequently, in 1993, the specification for the simpler and thus considerably faster protocol PROFIBUS DP (Decentralised Peripherals) was completed. First, the complex communication protocol Profibus FMS (Field bus Message Specification), which was tailored for demanding communication tasks, was specified. discrete or factory automation) and process automation. For this purpose, member companies agreed to support a common technical concept for production (i.e. The goal was to implement and spread the use of a bit-serial field bus based on the basic requirements of the field device interfaces.

The history of PROFIBUS goes back to a publicly promoted plan for an association which started in Germany in 1986 and for which 21 companies and institutes devised a master project plan called " fieldbus".
